I began my research by interviewing 4 people who work at FedEx to gain insight on misloads.
FedEx AR: Improving accuracy in FedEx warehouses.
Context
In Spring 2023, I had the opportunity to explore solutions to real world problems. After reflecting on my own work experiences I chose to explore improving accuracy rates of package handlers in FedEx warehouses.
Misloads, which are when packages are misscanned and placed in the wrong vehicle, was the most common issue I faced as a former package handler. Consequences include employee termination if misload counts were continuously high, wasted driver time and wages, wasted resources such as fuel and vehicle wear, and lower customer satisfaction since now their package is late.
Software
After Effects
Timeline
3 Months:
March – May 2023
My Role
• Interviewer
• UX Researcher
• Motion Graphics
Problem
Misloads cost FedEx millions of dollars a year to correct. How can we improve package handler accuracy?
Insights
1. Ring scanners are the current method used to record package placement, but they are an open-loop method due to their lack of verification. (gathered from personal experience and interviews)
2. Rough data average estimates, such as packages per vehicle, misloads per vehicle, and vehicles per warehouses. (gathered from interviews)
3. AR studies from GE and medical training, have shown a 46% increase in task acquisition speed as well as a 66% reduction in knowledge related errors.
4. 184 million is spent to correct misloads every year.
Solution
An application for AR glasses where packages are automatically scanned could be the hands free closed-loop method needed, since it can verify in real time the correct placement and display information. If FedEx implements a closed-loop method such as AR, they would save hundreds of millions of dollars currently lost on correcting misloads annually.
The goal of this prototype is to literally show package handlers where each package goes, with each truck having a designated color that corresponds with their packages.
Additionally, other delivery services such as UPS, USPS, and DHL use the same or similar open-loop practices, meaning that FedEx AR could be adopted in competitor warehouses, saving them similar amounts of money.
1. Interviews
2. Data Esteimates
Interview 1
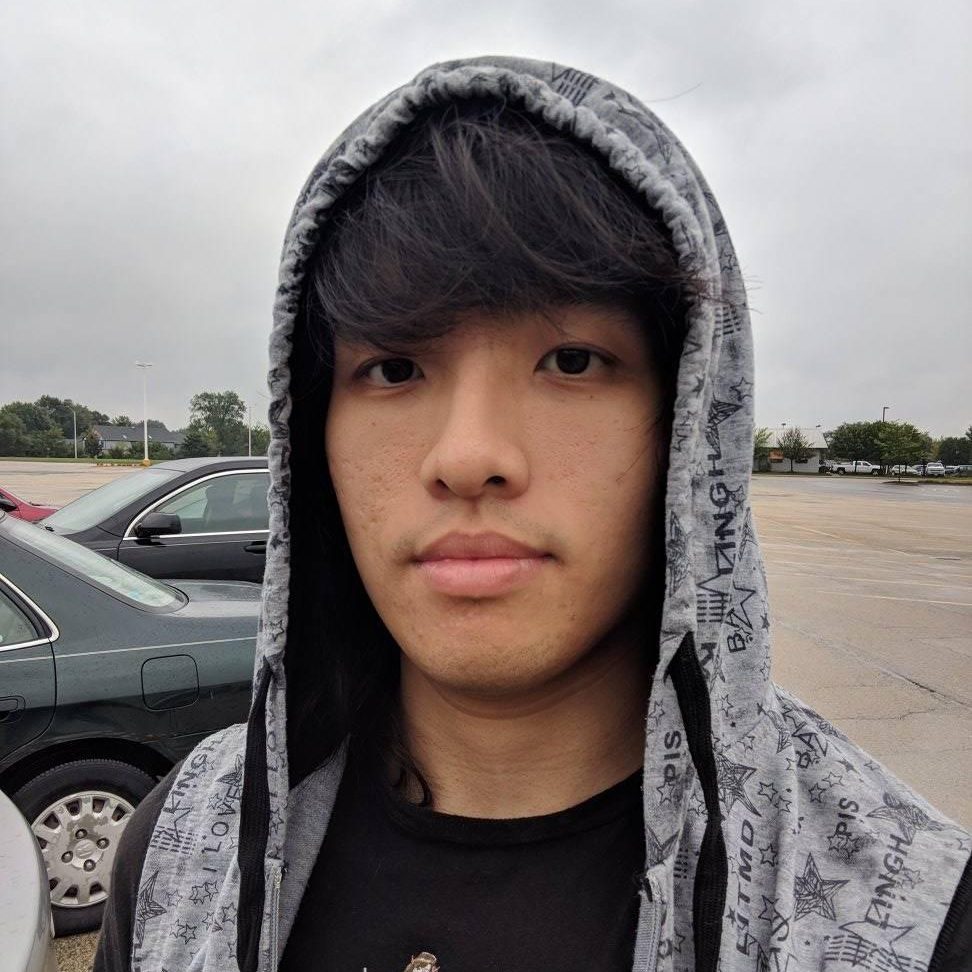
Sen L.
Operations Manager
6 years exp
Sen, an Operations Manager who manages package handlers loading trailers, stated performance and retention issues arise if package handlers are overworked. He also said that morale is mostly reliant on the attitude of their direct manager, and that unhappy or lazy package handlers tend to be more disorganized and have worse numbers, i.e. more misloads. He expressed that showing appreciation towards their hard work, such as positive reinforcement, basic respect, and bringing donuts or other treats, can help boost performance and retention. He stated however, that not all managers understand this, and that his job is more difficult when upper management is apathetic, not understanding, and / or overly critical.
Additionally, there is no efficient way of accessing information regarding trailers in different areas of the warehouse. This results in Sen walking from one side of the warehouse to the other in order to access a computer so he can look up trailer and package information, which happens multiple times a night and can take up to 15 minutes round trip.
Interview 2
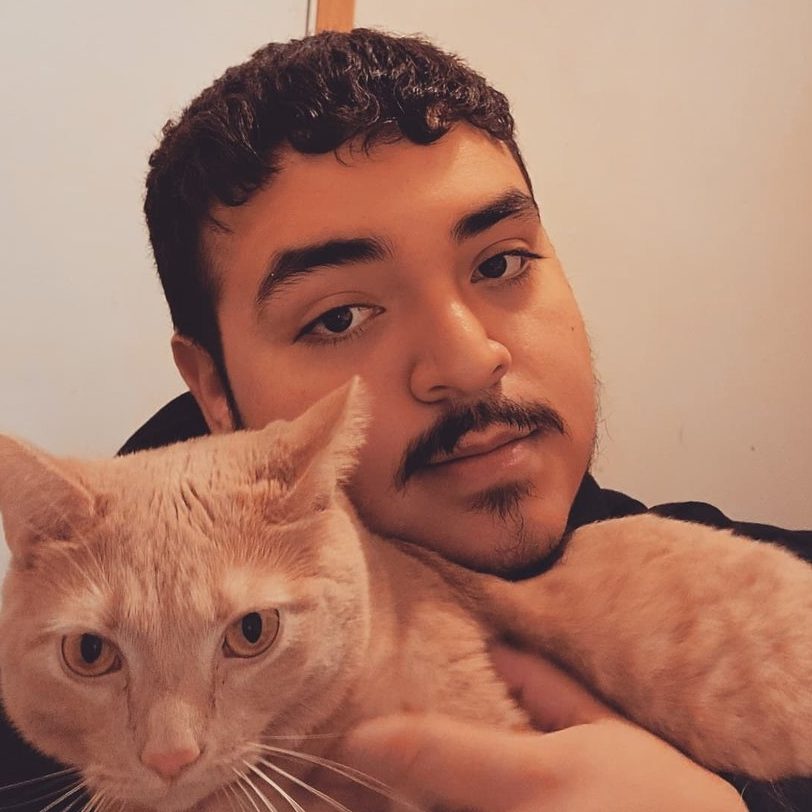
Jovanni M.
Operations Admin
6 years exp
Jovanni, who works as an Operations Admin where he takes care of damaged packages and labels, stated that there is no way for equipment to be tracked, leading to missing equipment which is sometimes even mistakenly left in trailers and sent to other warehouses.
He also expressed the same irritation as Sen towards inefficient information access throughout the warehouse.
Interview 3
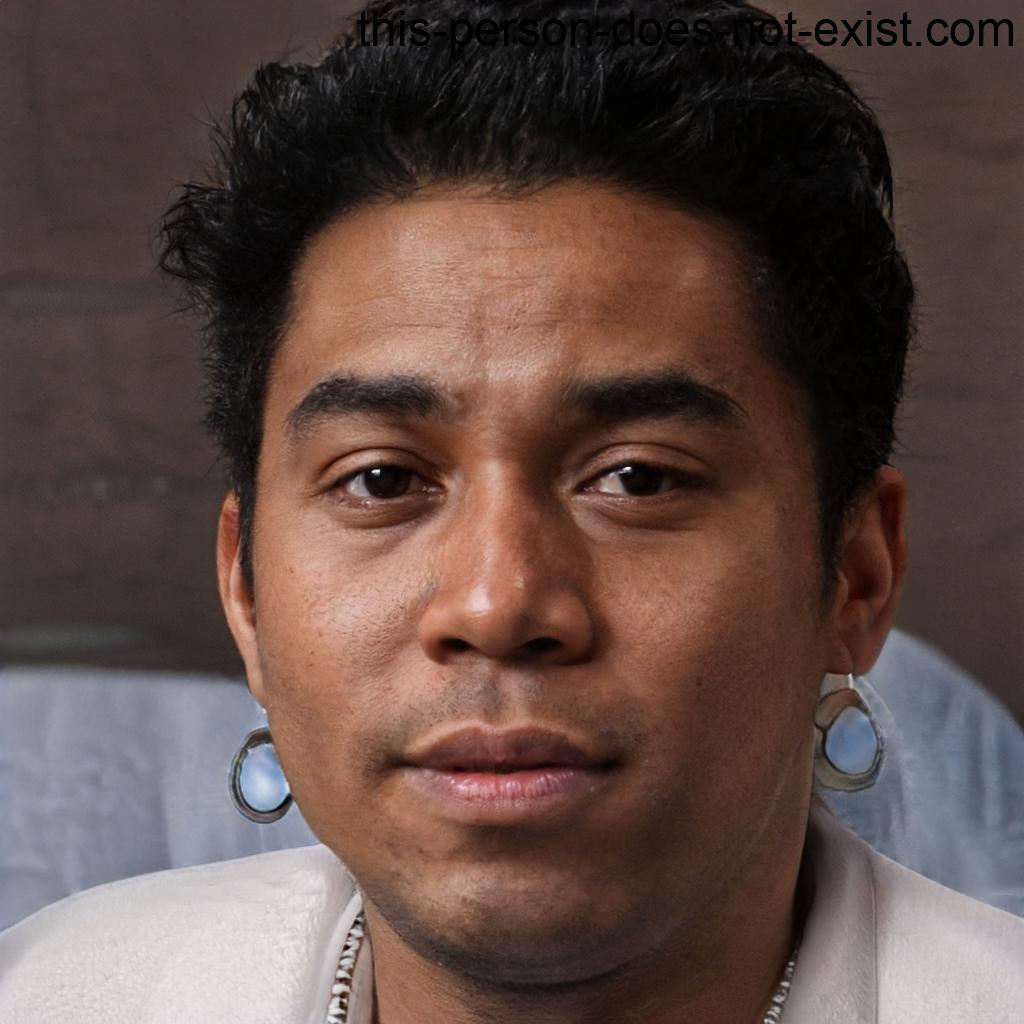
Mike M.
Operations Manager
5 years exp
Mike, who is an Operations Manager and former driver, stated that a common problem drivers face are unscanned packages not listed on daily manifestos. They often only find the unscanned packages while on their route, which results in driver frustration since now their day is longer than they expected. He emphasized that if package handlers were to use AR glasses, drivers would also reap the benefits since packages would be placed and scanned correctly.
Luckily for me, Mike also told me about the Nreal glasses he uses to watch shows and movies. While the Nreal glasses wouldn’t be compatible with FedEx warehouses due to being powered by a cell phone (package handlers are not allowed to bring their phones into the warehouses for security purposes), this got me thinking about what types could.
Interview 4
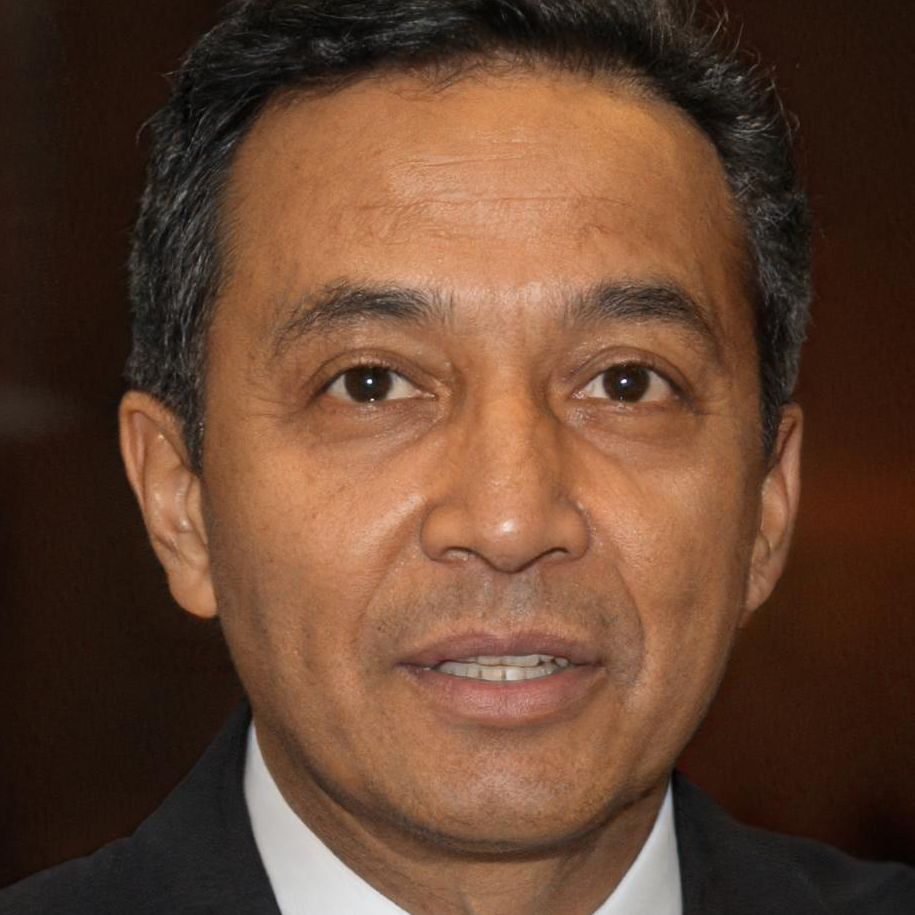
James S.
Operations, District,
& Corporate Manager
30+ years exp
James, who had worked for FedEx as an Operation, District, and Corporate manager for over 30 years, stated that AR glasses could automatically scan packages, replacing ring scanners altogether and closing the open-loop verification method. AR could also display package details, such as dimensions and weight, as well as identifying HAZMATs more clearly.
Although he no longer works for FedEx, he said that UPS, USPS, and DHL all use ring scanners or other similar logistics for recording their packages, and that those companies could also benefit from the same solution.
Additionally, he gave me rough average estimates for packages per vehicle, misloads per vehicle, and vehicles per warehouse, which I used to calculate annual misload expenses.
Insights
The main takeaways (inefficient information access throughout the warehouse, unscanned package issues, and AR replacing ring scanners) pointed to a correlation between lower package handler satisfaction and higher misloads, as well as a need for efficient information access, in which AR could solve.
These calculations were definitely the most difficult aspect of this project. I reached out to 10+ FedEx data scientists on LinkedIn, but unsurprisingly none got back to me. Thankfully, Sen and James were able to give me enough numbers and averages that I felt were workable.
Calculations were based on:
• Daily Misload Expenses per Warehouse (about one hour of extra driver labor)
• $24 (base pay) x 50 average vans / drivers = $1,200
• Daily National Misload Expenses
• $1,200 x 600 warehouses throughout America = $720,000
• Annual National Misload Expenses
• $720,000 x 255 business days = $183,600,000
I was utterly astounded by $183,600,000 being spent to correct misloads, which I would estimate is higher, considering gas, mileage, wear and tear on vehicles, and insurance costs. I did spend some time trying to obtain these numbers, however I realized early on that finding them would have been near impossible on just my own.
AR Studies
I began searching online for ways other warehouses improve accuracy rates, and came across two insightful studies.
The first was a 2017 GE study done with TeamViewer’s AR application “Skylight” and Google Glass, where “… increased warehouse task completion speed up to 46%.” was found.
The second was a 2021 ECMO medical training study where AR completion using Microsoft’s HoloLens 2 resulted in a “66% reduction in the number of knowledge-related errors.”, which points to AR “resulting in higher perceived clarity of information and information acquisition speed.”
These promising AR studies made me realize that AR could be utilized as the closed loop verification method needed to improved accuracy rates.
AR Glasses
While researching the best AR glasses for industrial use, Google Glass Enterprise Edition 2, was the top contender based on durability, battery life, controls, and price. Other runner ups were the Microsoft HoloLens 2 and Vuzix Blade. However, I learned that Google Glass Enterprise Edition 2 was discontinued in March of this year, with rumors of Microsoft HoloLens 2 also being discontinued soon.
This led me to look back on the last 10 years of AR glasses, where I noticed that many glasses have an unstable future (HoloLens) or have been discontinued (Google Glass) On top of that, the average price of AR glasses is about $3,000, meaning it would be unwise for a company to purchase AR glasses only for them to be discontinued a couple years after.
All of this made me think it would be best to focus solely on the FedEx AR application for this project, rather than a combined application and glasses approach.
Additionally, at the time of this project, Apple hadn’t released any information about their AR glasses. On June 5th however, Apple officially announced their AR glasses, and after taking a look, may very well be the top contender for FedEx AR based on durability, battery life, controls, price, and history of continued support for products.
Given my capabilities and project scope, I thought the best prototype approach would be to overlay shapes and UI elements using After Effects on package handler POV footage, illustrating how AR can guide package handlers to the right truck and location. I also wanted to include cumulative and individual van volume at the bottom right corner.
I reached out to my former coworker, Marchez Mack, who was still working at FedEx and able to obtain GoPro footage for me. He came in clutch, and I wouldn’t have been able to develop my prototype without his help.
Original GoPro footage by Marchez Mack
As I imported the footage into After Effects, I realized that motion tracking wasn’t able to be utilized, since the contrast was too low and perspective was too shaky. So, I tediously modified each individual keyframe of every component.
I was also hesitant because I wanted the elements to be as smooth as possible, but as I spent more time on the video, I realized that some choppiness actually works quite well, leveraging some authenticity to the prototype.
First draft.
Once I had a prototype draft, I reached out to my interviewees for their critique.
More package detail was the biggest feedback, such as weight and dimensions, as well as extending the directional AR element further into the van.
I changed the first truck color to green, added package dimensions, and included an automatic barcode scanner verification.
Additionally, I extended the path guide further into the truck.
Final Prototype Cut.
The main things I struggled with were the calculations (which I did get some tutoring and help for), but I also struggled with trimming things down so my pitch would be within a reasonable time. Presenting enough information succinctly is always difficult, but I feel that this project helped me improve that skill.
My biggest regret is not exploring further how FedEx van drivers are actually employed by independent contractors who purchase their routes from FedEx. I wish I noticed this pivotal information much earlier because this means that the annual $184,600,00 spent on misloads is split to some degree between the FedEx corporation and independent contractors. Unfortunately, it was late May by the time I realized what I overlooked, and I did not have enough time to pivot. I wonder what the real breakdown of all these costs are though and how it impacts dynamics between the FedEx corporation and independant contractors.
That being said, I’m still happy and proud of this solo project. I feel my presentation skills were improved, and I was able to explore an intrinsically interesting problem that I had personal experience with while brainstorming solutions derived from interviews and research. I also LOVE using After Effects, so I’m happy to have been able to utilize those skills as well!
MORE WORK
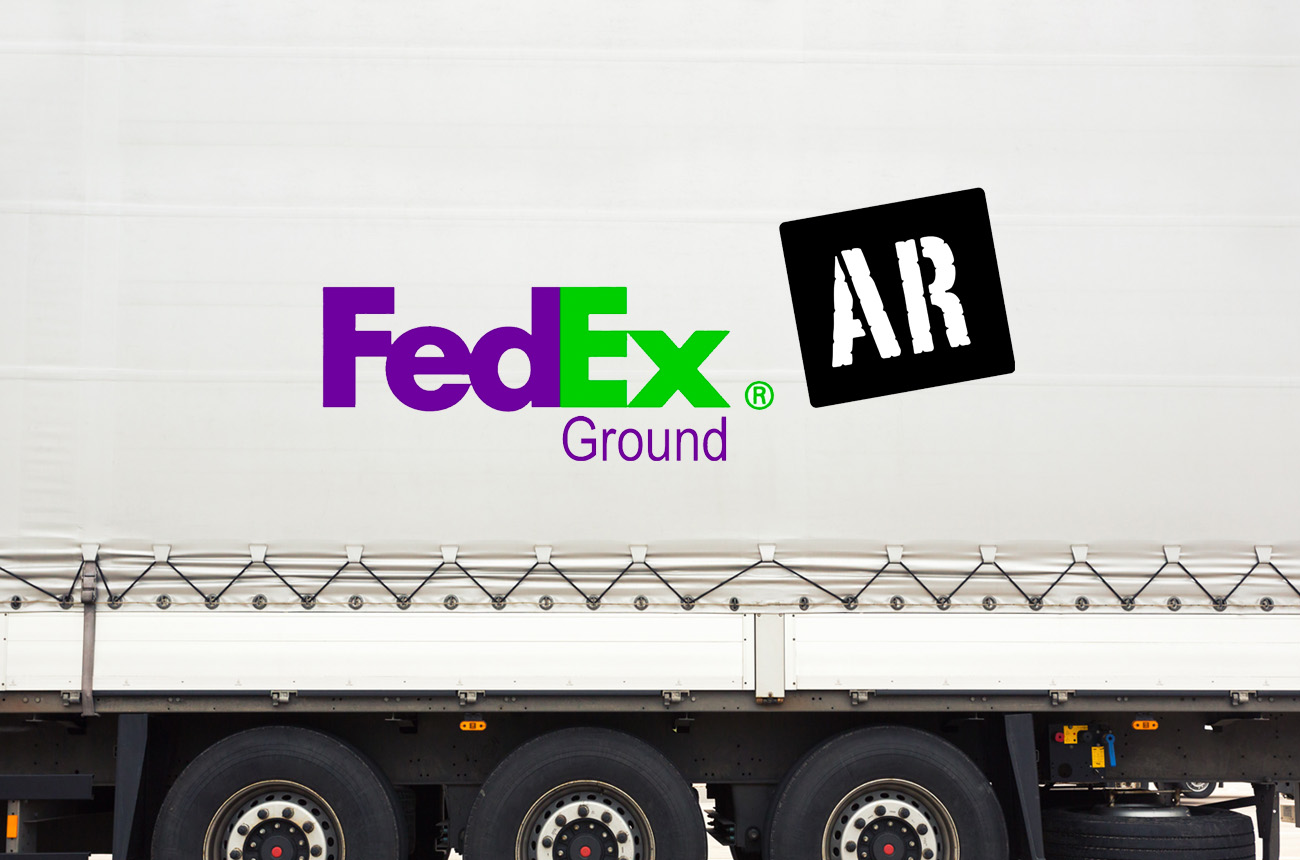